Inventory management is defined as a complex set of measures aimed at ensuring the highest possible level of customer service while minimising the ongoing costs associated with maintaining inventory. And, as practice shows, it is a headache for almost every company involved in trade or production.
Inventories inherently link the processes of producing and selling products.
The main purpose of inventory management is to ensure that products are produced in the right quantities and on time, and that manufactured products are sold in full, while minimising inventory costs.
If a company has large stocks of inventory, it is very bad because it is frozen cash and these stocks do not increase in value but lose it over time due to deterioration in quality. This does not apply to wine and whisky, of course.
Inventory Management Systems
There are two classes of inventory management systems: single-period and multi-period. This classification is based on the nature of the decisions to be made. We will not consider these systems in detail here, but we will briefly discuss each type.
Single-period systems are characterised by a one-off purchase, where the stock is intended to last for a certain period of time and the products in question are not reordered (for example, the decision of a newsagent to buy newspapers and magazines for his shop). Buying little means a loss of income, buying a lot means the risk of unrealised goods and consequently losses, because nobody needs yesterday's newspapers.
There are two main multi-period models of inventory management systems:
- A fixed order quantity model (EOQ or Q model)
- A Fixed Period model (P-модель).
These management systems ensure that certain goods and raw materials are available throughout the year. What is the difference between them?
In the fixed-order-quantity model (Q model), an order for the delivery of an item of stock is created when the remaining stock of that item falls to a certain level. This event can occur at any time when the level of remnants falls to a certain level.
In the P-model, the next order is placed after a predetermined period of time.
Main Differences Between Q and P Models
Features
Fixed
order quantity model (Q model)
A Fixed Period model (P model)
Order volume
Q is a constant value (the same quantity is ordered each time) |
q is a variable value (changes with each subsequent
order)
The moment of the order
|
T - at the end of a predetermined fixed period of
time
Stock level recording
|
Only at a preset time to control inventory levels
Stock level
|
Larger than a fixed order size system
Maintenance difficulty
|
Type of products
|
No matter what system you use, you face two problems:
· Controlling each inventory item;
· Maintain and track inventory status
Can a Business Operate Without Inventory?
In the real world, companies need to have some inventory of raw materials and goods. Nobody knows what will happen in the future and when they will need what. The just-in-time system, which provides for almost zero inventory of products, is not feasible in today's business environment.
Unfortunately, we cannot anticipate our customers' needs. The modern business environment means that customers do not like to wait, and if we do not have the product they need, they will order it from our competitors and we will lose sales.
To stay in business, you must always have the goods on hand. The same goes for raw materials for production. We cannot guarantee that our supplier will deliver everything on time. Rarely does the production process run smoothly and the production plan is executed on time. Another factor is that our suppliers require us to purchase certain quantities of goods or raw materials from them in order to receive a volume discount.
You are not alone. The wholesaler probably suffers even more because he has to buy more goods from his supplier to get a discount. A manufacturer cannot produce and sell products in small batches. To be economically viable, he must produce a lot of goods, which are not all bought by all buyers, so he also has a growing inventory.
Despite their cost, inventories are a necessary part of keeping production costs low.
Companies that try to drastically reduce their inventories usually regret it very much, which leads to disaster and a drop in sales.
Failure to predict customer demand leads to either overproduction of goods or the production of unsellable goods. Such goods have to be accounted for somehow, and accounting rules dictate that inventories be carried at the lowest cost, and you have no benefit from them until you sell them. At the same time, inaccurate demand forecasts lead to even larger inventories, which then turn out to be of no use to anyone.
Universal ABC Analysis
Any inventory management system should indicate when to order a material and how much to order. With a large nomenclature, it is not possible to analyze every item in the nomenclature. To simplify this problem, an ABC analysis is performed.
The method is based on the well-known "Pareto rule" mentioned above: 20% of the effort produces 80% of the result and vice versa.
The purpose of this analysis is to provide a simple and clear ranking of resources, which will allow you to set priorities, identify bottlenecks, and take corrective actions in a timely manner.
The analysis is based on the principle of classifying resources into three groups:
Group A - the most valuable;
Group B - intermediate;
Group C - the least valuable.
Regardless of the area of application (production, trade), the ABC analysis is performed in the following order.
1. Select the object to analyze:
- Material nomenclature;
- Assortment of goods;
- ...
2. Selecting the parameter to analyze:
- Revenue in monetary terms;
- Sales volume (quantity);
- Return on sales in percent;
- ...
Which criterion to use to select these 80% - profit or sales - depends on the purpose of the analysis. If profit is the basis, we rank inventories by marginal revenue. If sales, then by turnover (volume of products sold).
An ABC analysis of the finished goods (merchandise) assortment might look like this).
Name
Value, CAD
Share
(contribution), %
Savings
Deposit, %
Group
Product 1
1200
40
40
А
Product 2
900
30
70
B
Product 3
500
17
87
B
Product 4
200
7
93
C
Product 5
100
3
97
C
Product 6
100
3
100
C
3000
100
100
C
Expenses Increasing Inventory Costs
Axiom: Costs always rise as inventory levels increase
The initial cost of inventory is easy to determine: just take the supplier's price multiplied by the quantity, add the company's overhead for shipping, and you have the cost price. But is it that simple?
After the inventory arrives at our warehouse, the company begins to accumulate costs for storage, insurance, accounting of this inventory, movement of inventory within the warehouse and between warehouses. Some inventory deteriorates and loses its value, which is also a cost to the company. Such costs may not be included in the cost of inventories, but they are included in the calculation of the financial result.
Inventory Storage Costs
This category of costs includes the costs of maintaining storage equipment and facilities, insurance and costs associated with petty theft and losses due to non-use of frozen inventory.
These costs are usually fixed and do not depend on the number of storage units (SKUs), on the number of incoming or outgoing shipments.
Typically, these costs increase when storage space is full and there is a need to purchase or lease new warehouse/storage space.
The more warehouses a company has and the closer they are to consumers, the faster customers are served and the lower the transportation and freight costs, although this is not always the case.
But it is safe to say that more inventory leads to higher storage costs.
Accounting and Controlling Costs
The following items are included in these costs
- Computers;
- Software;
- Staff for purchasing, receiving, quality control, and accounting.
If the existing system is working efficiently, an additional unit of storage will not increase costs. They may be caused by the need to replace software, purchase a new computer, or hire a new employee.
Inventory Spoilage or Obsolescence
Most companies never use 100% of their inventory, and some of it either spoils or becomes obsolete. In most cases we can remember the Pareto rule - 80/20. 80% of the company's current turnover is provided by 20% of the goods. The remaining 80% of the goods are in the backyard, waiting for a better future. The company wants to get rid of such goods, but such an operation involves certain difficulties:
- Taxation;
- Increase in the company's expenses, which affects the financial result.
Slow turnover or its absence absorbs the company's resources and reduces the efficiency of its activities.
Accounting Effects on Inventory Costs and Cash Flow
Businesses can use one of two existing inventory accounting systems: periodic or continuous inventory accounting.
The periodic accounting system is more common among small enterprises. The essence of such a system is as follows:
Receipts and dispositions of inventory during the accounting period are not reflected in the inventory accounts. At the end of the period, an inventory is taken and the cost of the inventory sold is determined by the formula:
CP = Cp +C-Ck, where
CP - cost of sales of inventories
Cp - cost of inventories at the beginning of the period;
C - cost of inventories purchased during the period;
Ck - cost of inventories at the end of the period
The general scheme of
periodic inventory accounting is as follows:
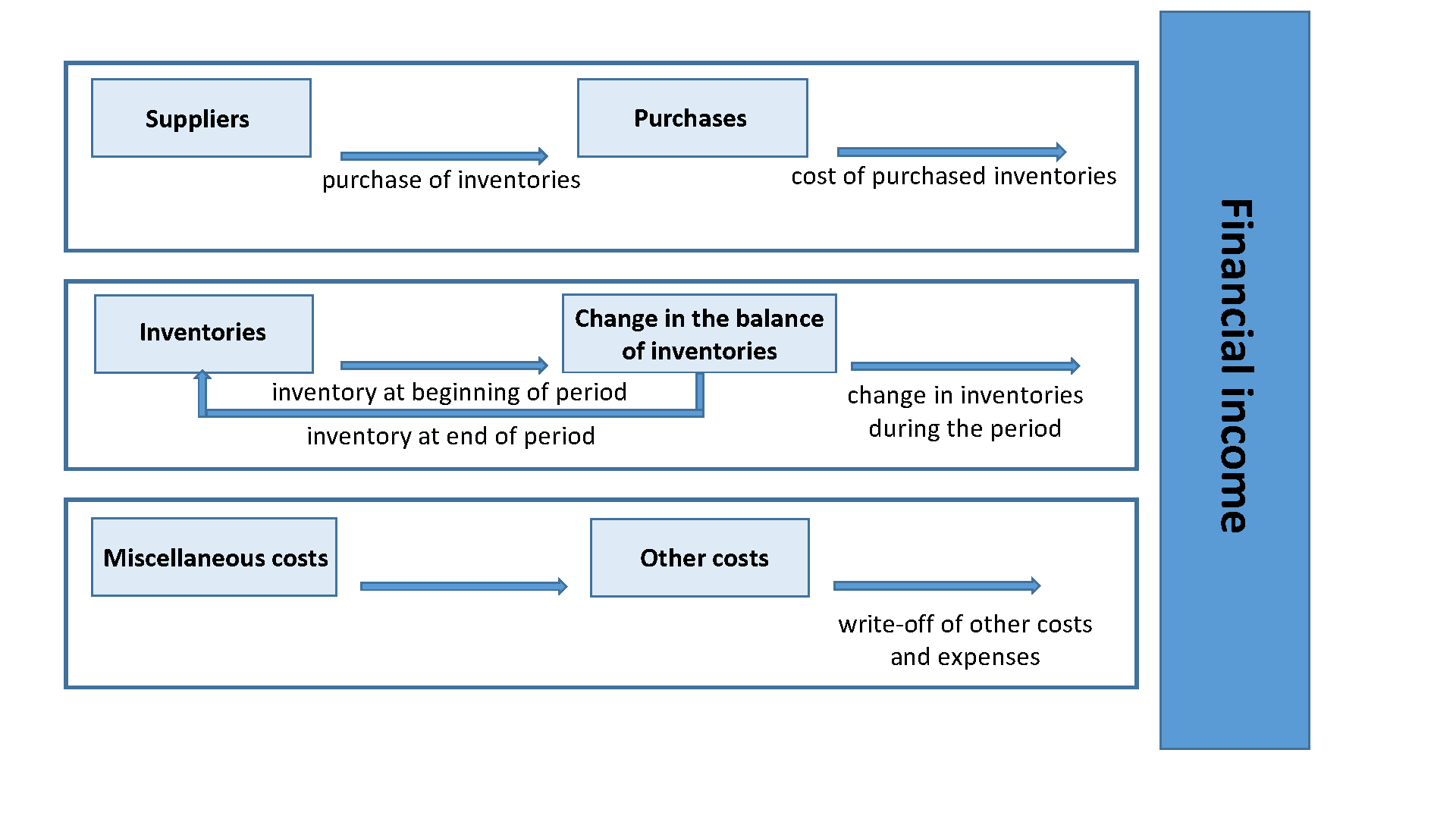
The perpetual system of inventory accounting provides for the display of inventory movements on the accounting accounts.
However, regardless of the inventory accounting system used, the company should determine how it will estimate the cost of inventory, since the cost of receiving inventory in different periods is different.
The question is not trivial. Accounting is a very inexact science. And if you ask five accountants to calculate the cost of inventory at the end of the period, you will get five different answers.
Accountants can manipulate the calculations and get different results depending on management's goals. It is easier for retailers, but manufacturers can consider a much larger number of metrics: labor, materials, and overhead.
There are the following methods of determining the cost of inventory:
1. Specific identification method;
2. FIFO;
3. Weighted-average-cost method.
Depending on the method chosen, the cost of inventory at the end of the period may differ, sometimes significantly.
In Summary
Inventory management is a tricky and tedious business. Reducing inventory requires a good knowledge of the business and is a major challenge for most companies. It is also undeniable that companies spend a lot of money on creating and maintaining inventory, and in order to be more efficient, companies need to think about inventory optimization, which also has a positive impact on their cash flow.