When we deal with the production of goods, we cannot dispense with the use of the Manufacturing module and its integral component, the BOM. The production of goods is called a process when you need to make another product from one product or material, and it can be either a simple assembly of two or more complete products to be sold as a separate set, or a fully fledged complex process of making goods from parts, with all the shops, processes operations, and step-by-step instructions.
A document that lists specific components along with their respective quantities, as well as the sequence of manufacturing operations required to produce them, is called a Bill of Materials (or BoM for short).
Settings of BoM in Odoo 17
In order to set up BoM correctly in Odoo 17, we should first make sure that you have made all the necessary preliminary settings for production.
First
of all, we should check whether the production centers through which the goods
pass during the production process are configured, and if we plan not only to
track components in the manufacturing process, but also to work with production
operations and track work, then we should also enable the Work Orders option in
the general settings of the module.

If we subcontract certain components necessary
for our production to other companies for manufacturing, then you should also
enable the Subcontracting option in the general
settings of the module:
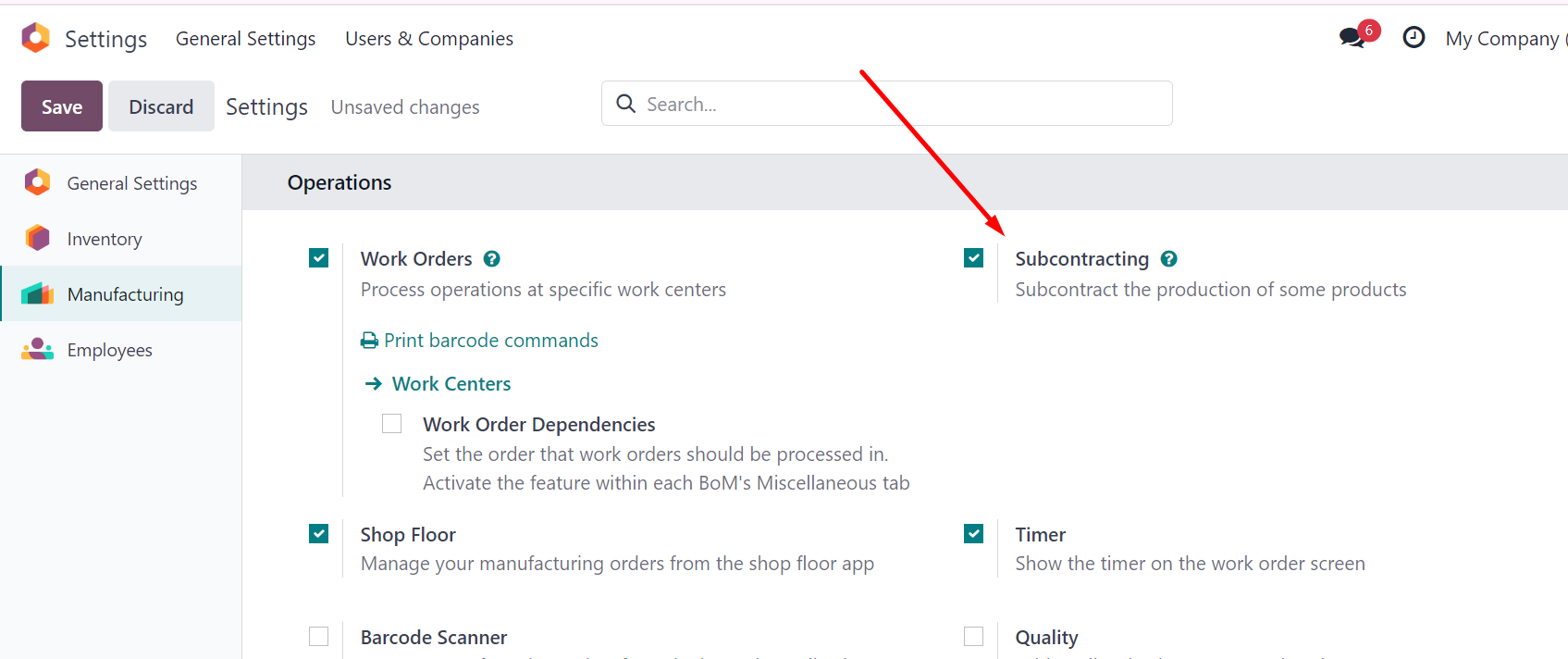
If we receive
by-products during the production of a product, we need
to enable the By-products option in
order to reflect this in the system.
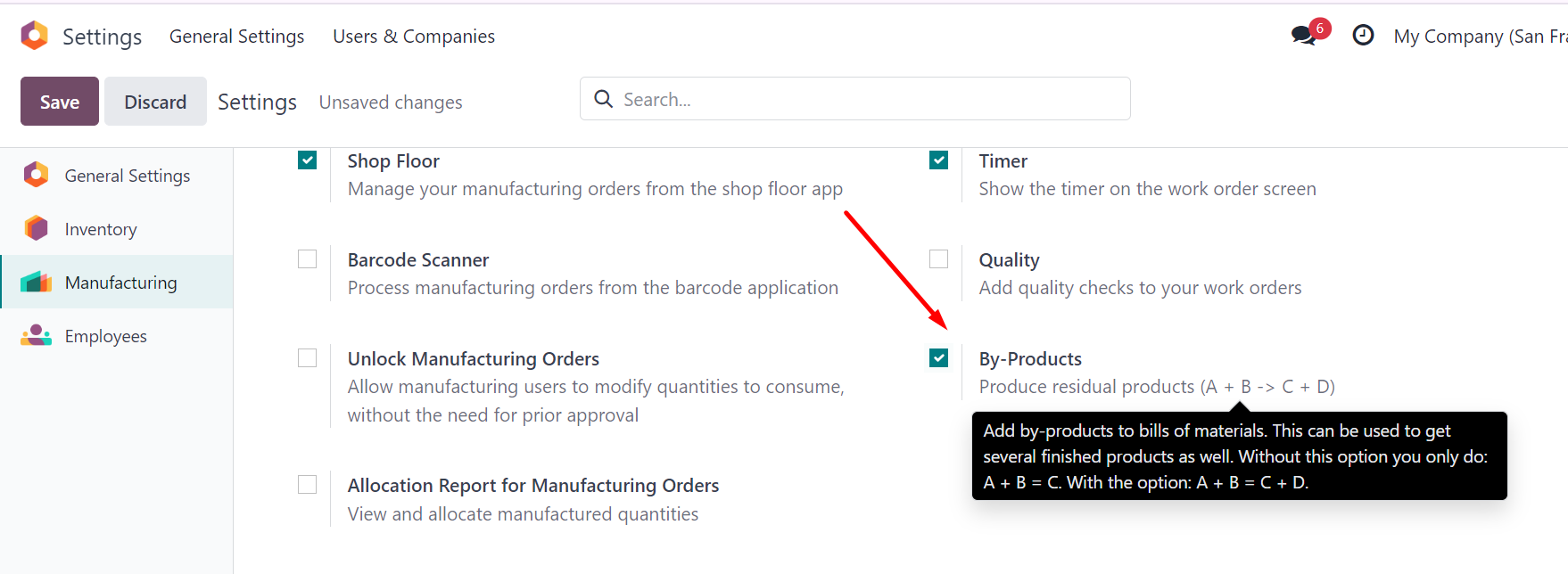
It is also important to remember that the product that is being manufactured must have the appropriate Manufacture route, i.e., in the product card on the Inventory tab, you must mark that it is a manufactured product:

and if we plan to keep records by lots or serial number, then these options should be specified by checking the appropriate checkboxes.
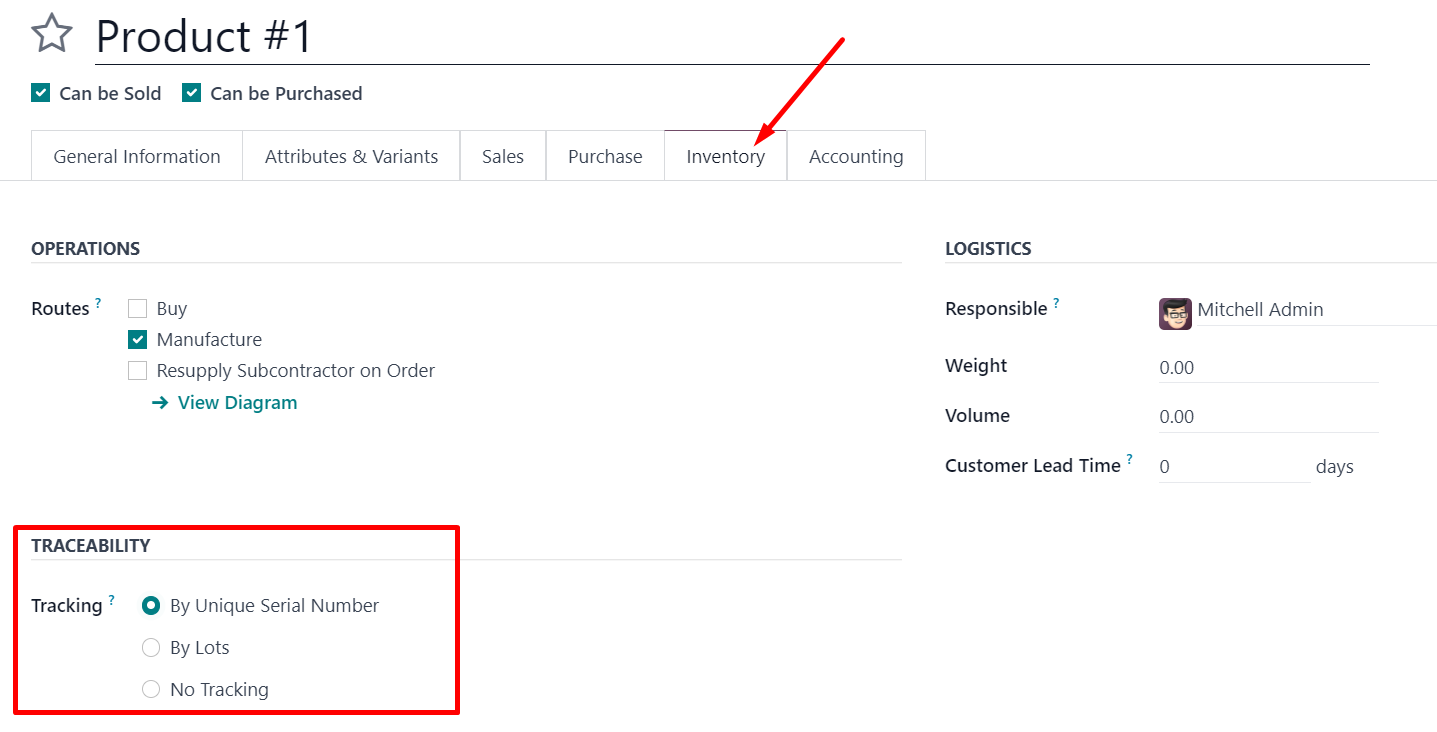
If all these settings are correct, we can configure the BOM for the goods we want to produce.
There are several ways in which we can create a new specification:
-from the menu of the Manufacturing
module
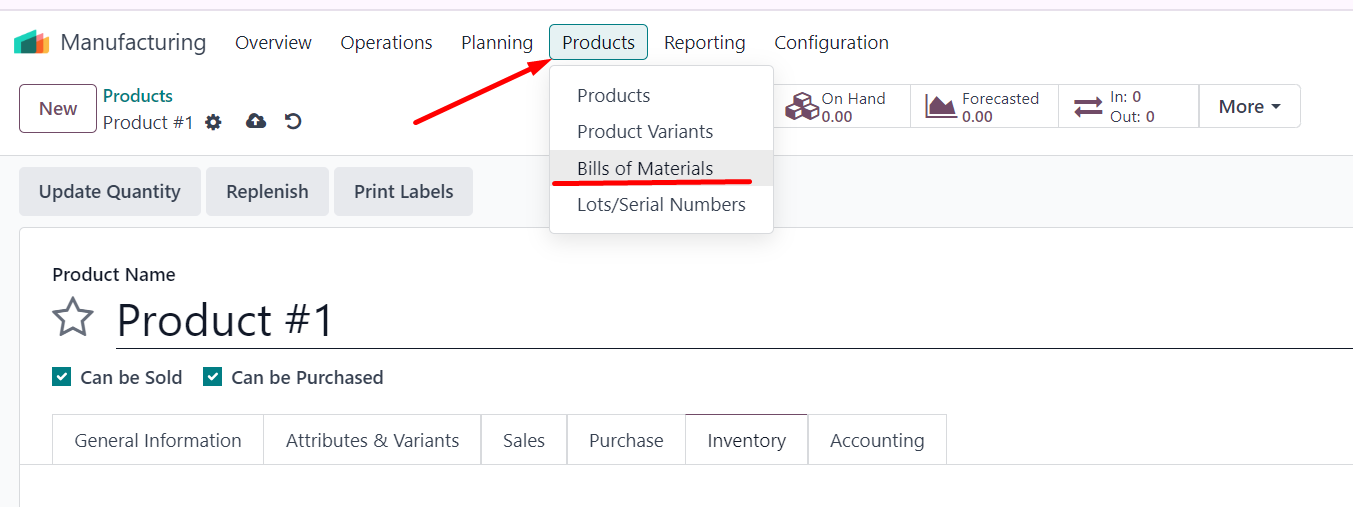
- or via the smart button from the product card
through the Sales, Inventory, and Manufacturing modules.
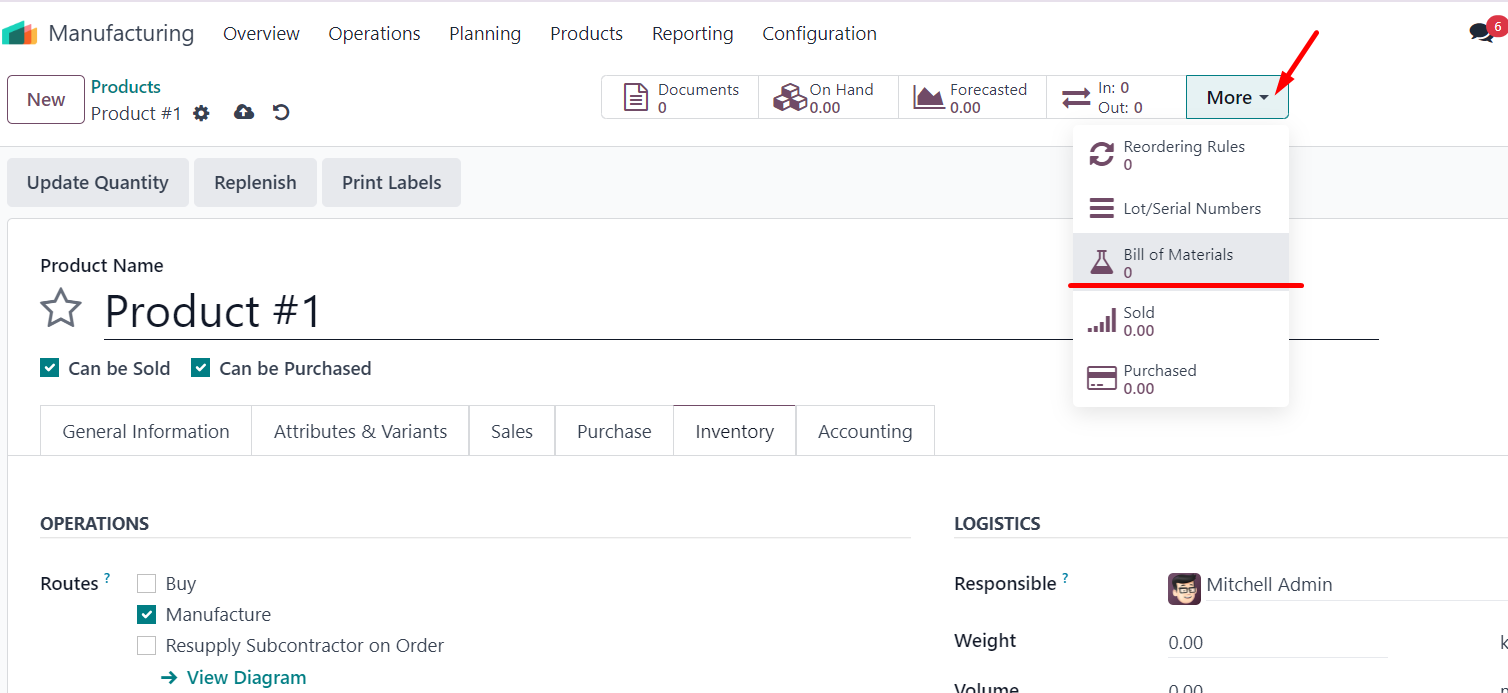
When creating a new
BOM, we need to fill in the following fields:
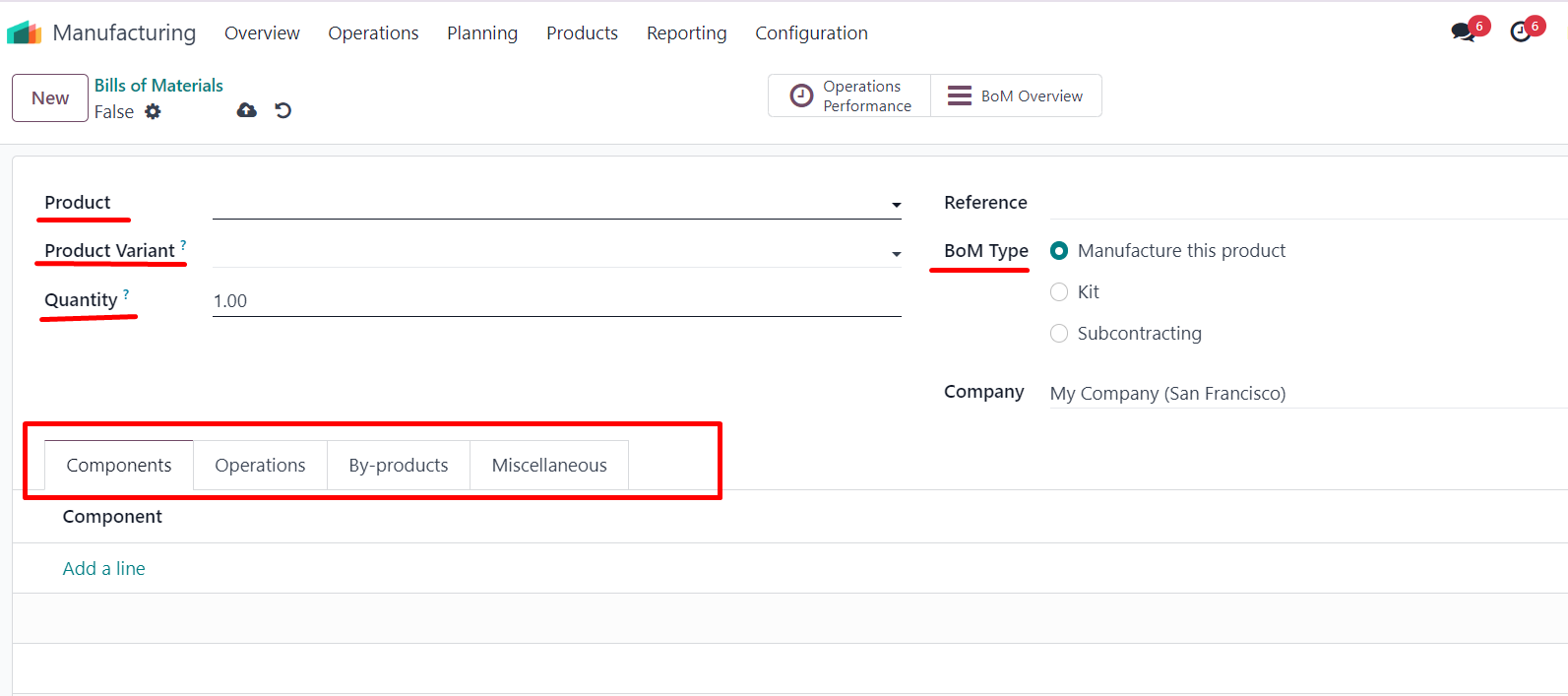
- the name of the product we are manufacturing
- If we are going to use product variants for this product, then we will specify the product variant
-the number of units of the finished product that we will receive at the end of the manufacturing process from the components specified below.
-specify the type of specification. For goods that are manufactured, the specification type Manufacture this item should be selected. The Kit specification type is used for sets of goods, and the Subcontract type is used for goods or components that we manufacture with the help of contractors (we give the contractor certain components to manufacture and we get the goods we need back).
The next thing we need to specify is the components we use for production. Components can also be goods produced as a result of another production process.
BoM in Manufacturing
Let's take a look at a specific example of how to set a BoM for the production of a specific product.
Let's say we're making a product called Table.
To make it, we need the following components:
- Table Top -1 unit,
- Table Leg – 4 units,
- Bolt -4 units
- Screw-4 units
We will also have an operation called Assembly, which is performed in a work center called Assembly Line 1; the operation takes 60 minutes; you can optionally add a work instruction to the description of the operation, for example in pdf format.
We do not receive any by-products at this stage of
production.
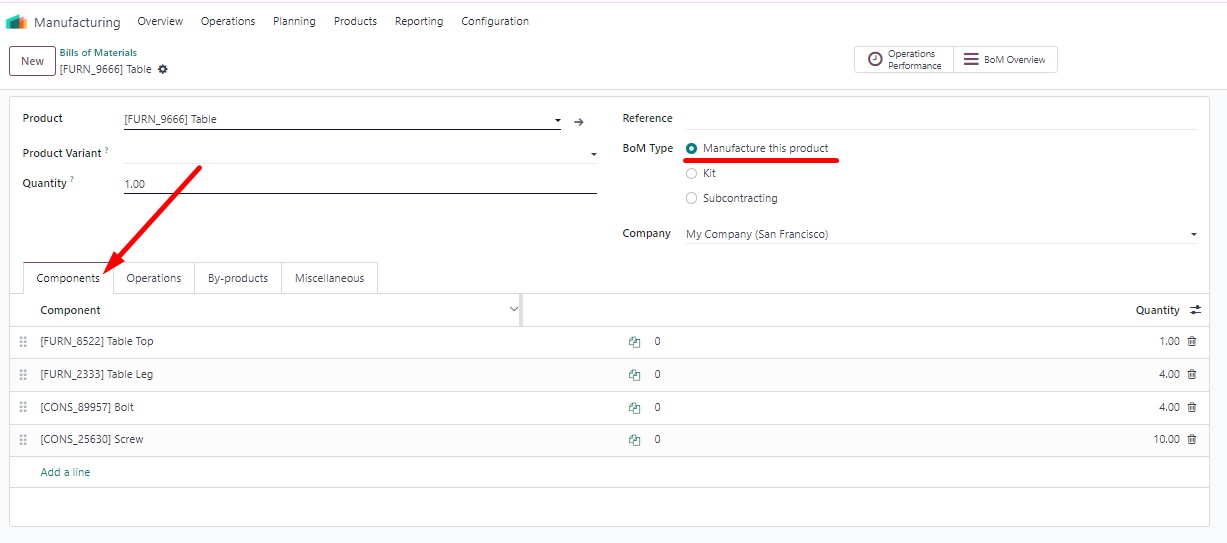
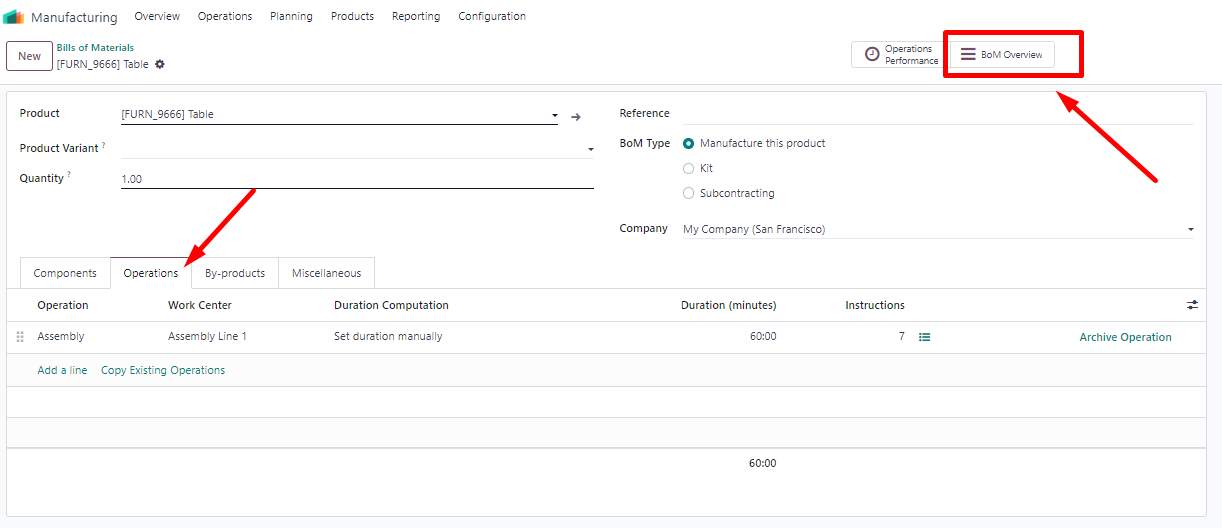
If we go through the smart button and look at the created BOM, we will see the following structure, with the cost of components, operations and goods, as well as information on the availability of components.
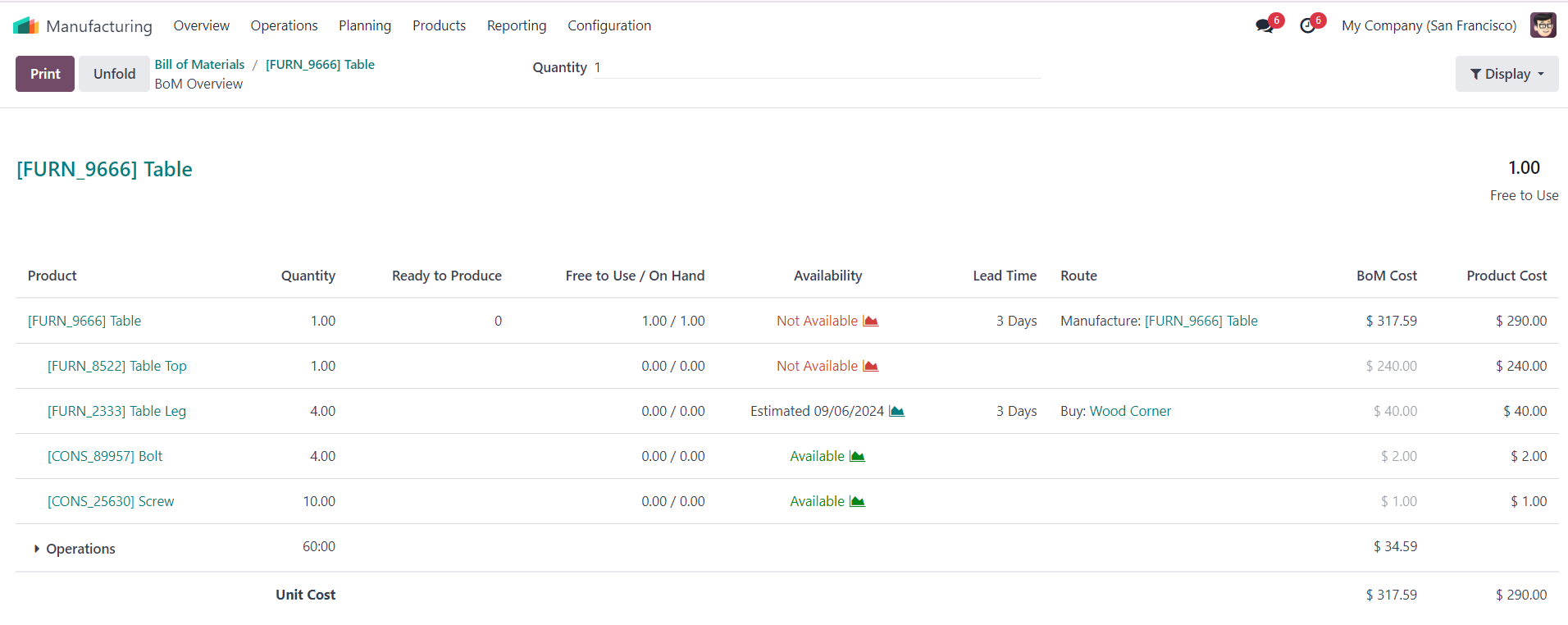
Let's add another specification for the Table top. Let's say we don't have a paint shop and we have a subcontractor do this work for us, that is, we ship the Wood panel to the subcontractor and they ship the painted surface back to us.
For those products that we outsource to a
subcontractor, you need to specify the appropriate route " Resupply Subcontractor
on Order" in the product card settings on the Inventory tab.
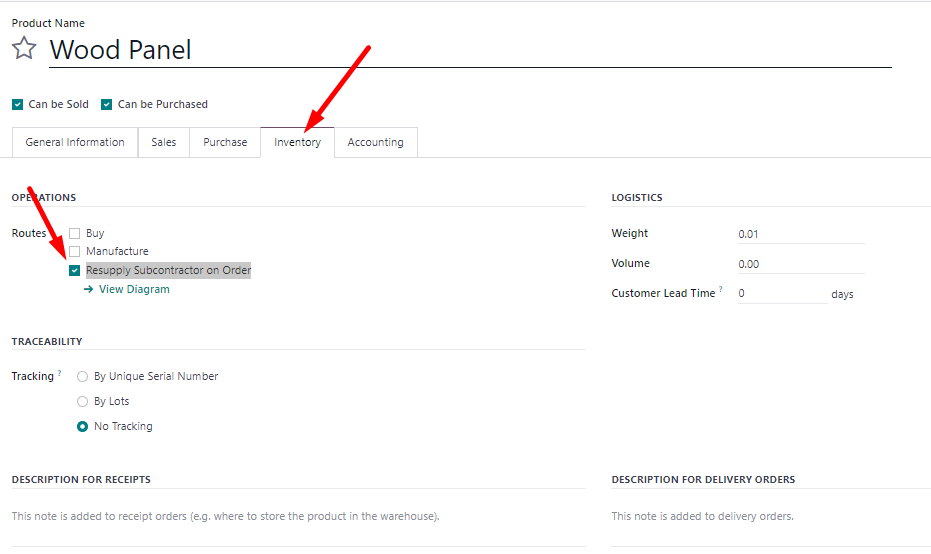
So, our specification for Table Top will look
like this:

Now let's make a specification for our Wood panel. We will make it from Wood Log. We do this by using the Sawing operation in the Sawmill
Station 1 and let's also specify that during the manufacturing process we
will get an additional product called Child's
Sword in the amount of 2 units (let's assume that we will get it from
scrap). This is what our specification for Wood Panel will look like:
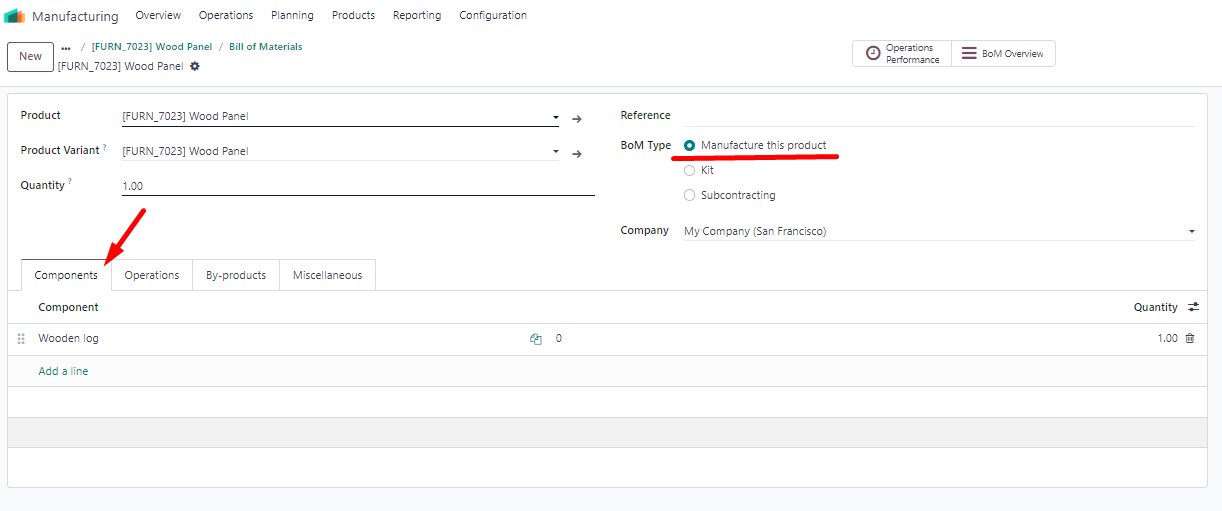
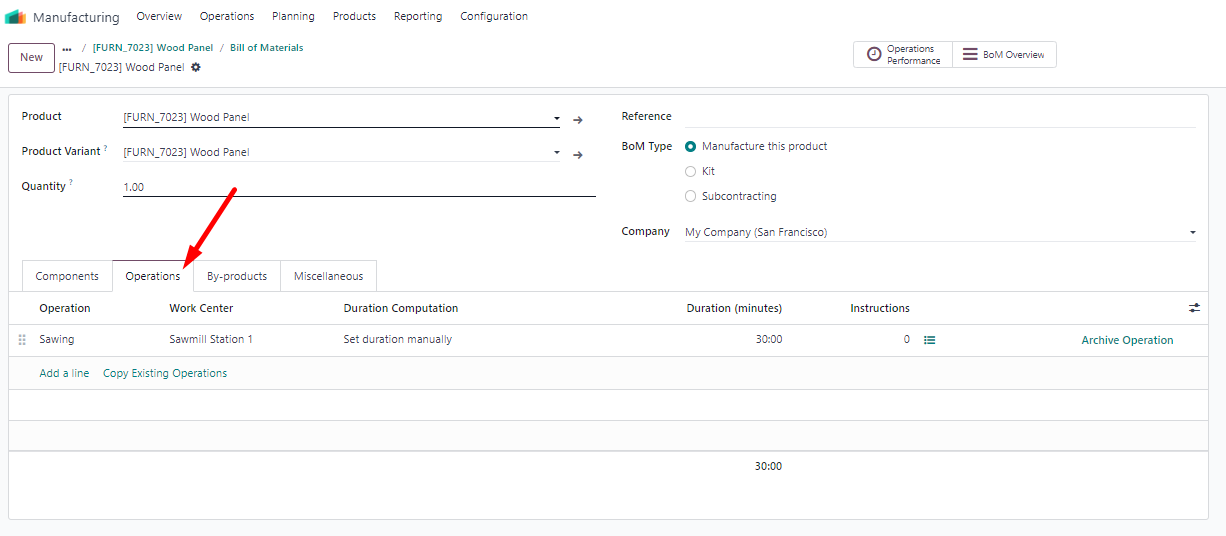
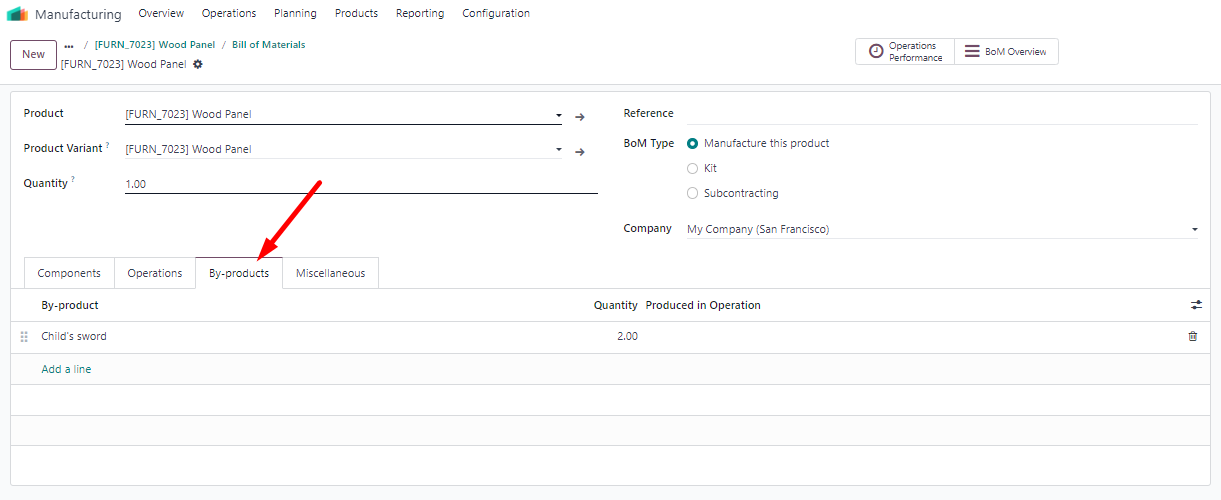
Now let's take a look at what the specification
of our Table looks like. As you can see, we have a rather complex three-level
specification with components, by-products, and operations.
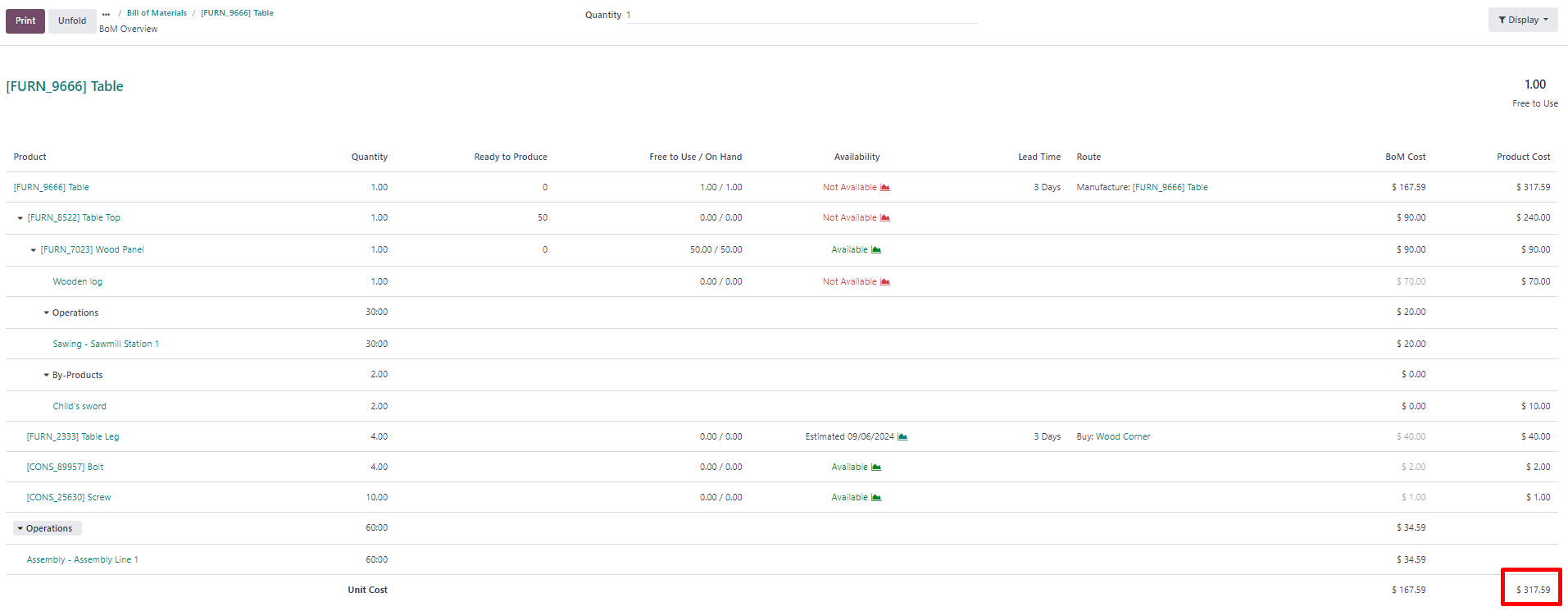
The cost of the product that we produce is calculated
based on the BoM and if you set the costing method for this product to AVCO or
Standard price, then its cost will be automatically recalculated from the BoM
based on the cost of the components and operations that were involved in the
production. In fact, if we go to the product card of the Table we produced and
recalculate the cost from BoM, we get the same cost as we see in the BoM
structure in the previous screenshot:

BoM for Kit
There is another type of specification called a “Kit”. In fact, a kit does not involve any production as such and is used mostly for the convenience of warehouse operations. When we sell some products in a set with other products. For example, a promotional set that includes a large mug + a pack of Indian tea.
The BoM of
such a Kit looks as follows:

To demonstrate how this affects warehouse operations, let's sell such a kit through the Sales module and see what information is displayed in the delivery transaction.
We
created and confirmed the sales order for the sale of such a kit, and we
immediately had a delivery transfer:
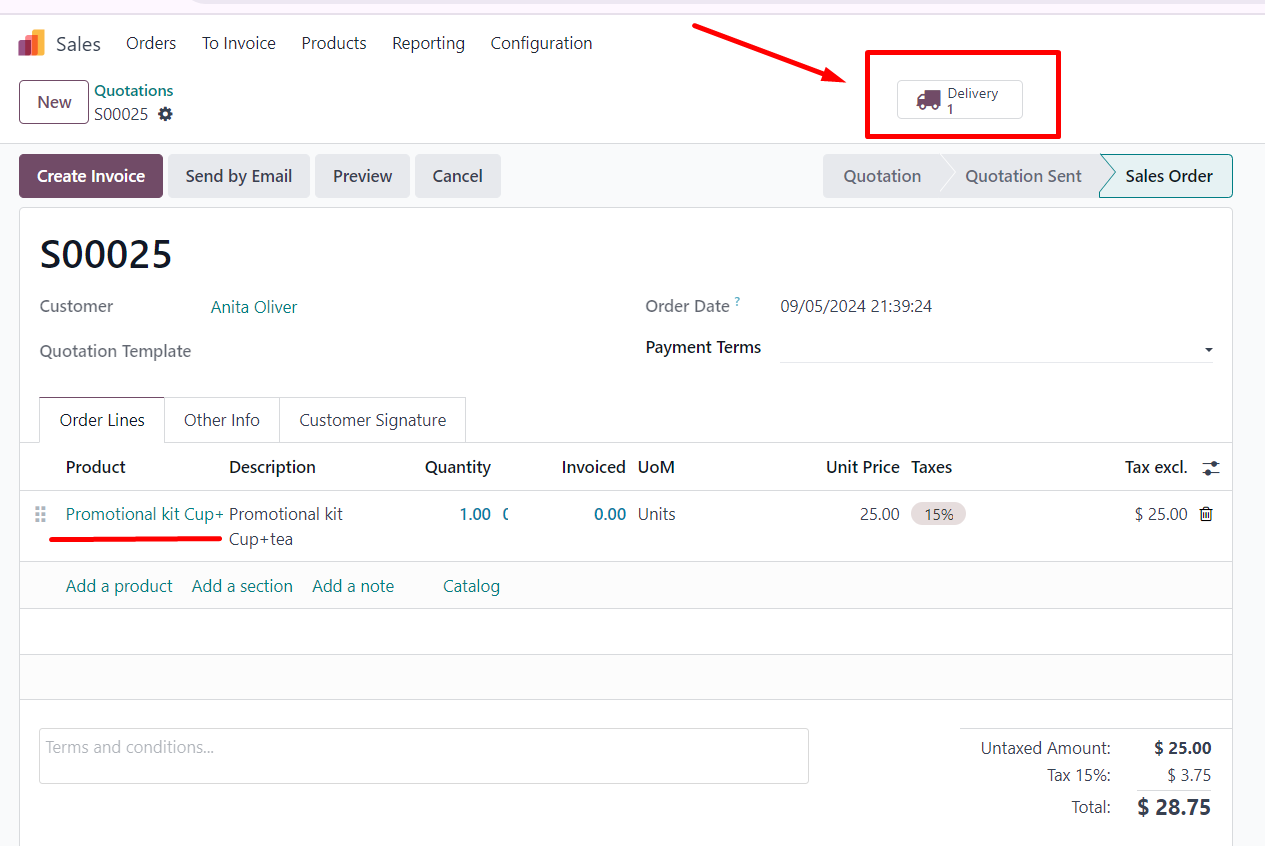
When we go to Delivery, we see that the delivery
status is Pending Shipment, and among the items for which a delivery has been
created, we see components, each of which is part of our kit:
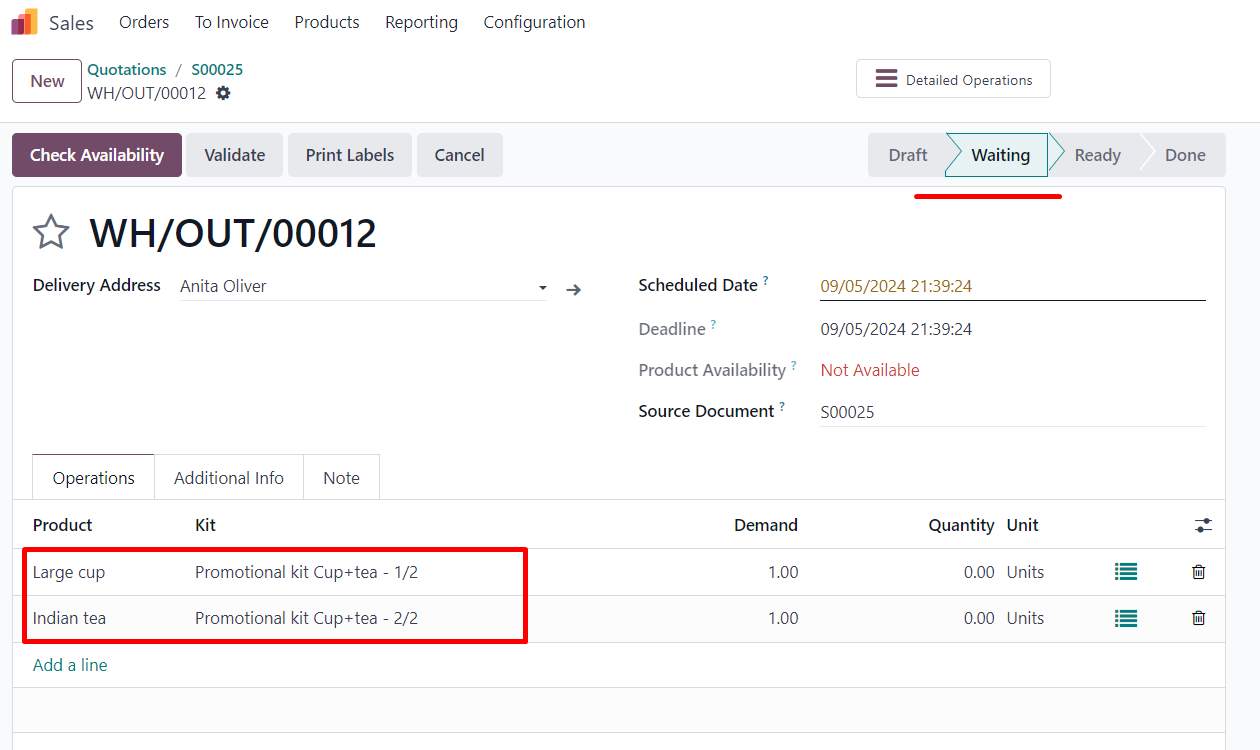
This means that there is no actual production taking place, just an instruction to our warehouse to assemble the product from two components. Kits are convenient when we sell sets of different products and need to write them off. It also works both ways - we can buy kits of goods and later sell their components separately.
So we've looked at all three types of BOMs and used a practical example to see how they are used in production.